Gas Assist Injection Molding
Get Higher Quality Components and Lower Costs
We inject nitrogen gas into the hot melt stream during the molding process, displacing the resin in thick-walled sections, to create a hollow core. This innovative process is ideal for several important reasons:
- Increase Design Options: Since this process is not constrained by typical tool design requirements, parts with complex designs can be produced with less complicated tooling.
- Improve Part Quality: The Gas Assist process creates uniform pressure throughout the part which minimizes any potential warp issues. The technology can also be used to eliminate sink marks at rib and boss locations. Parts with varying wall thicknesses can be molded without the need for complicated cores.
- Reduces Costs: Since Gas Assist parts require less material and run at faster cycle times the corresponding piece prices are reduced accordingly.
- Part Consolidation: With gas assist molding, several components that would normally be produced separately with conventional injection molding can be combined into a single part.
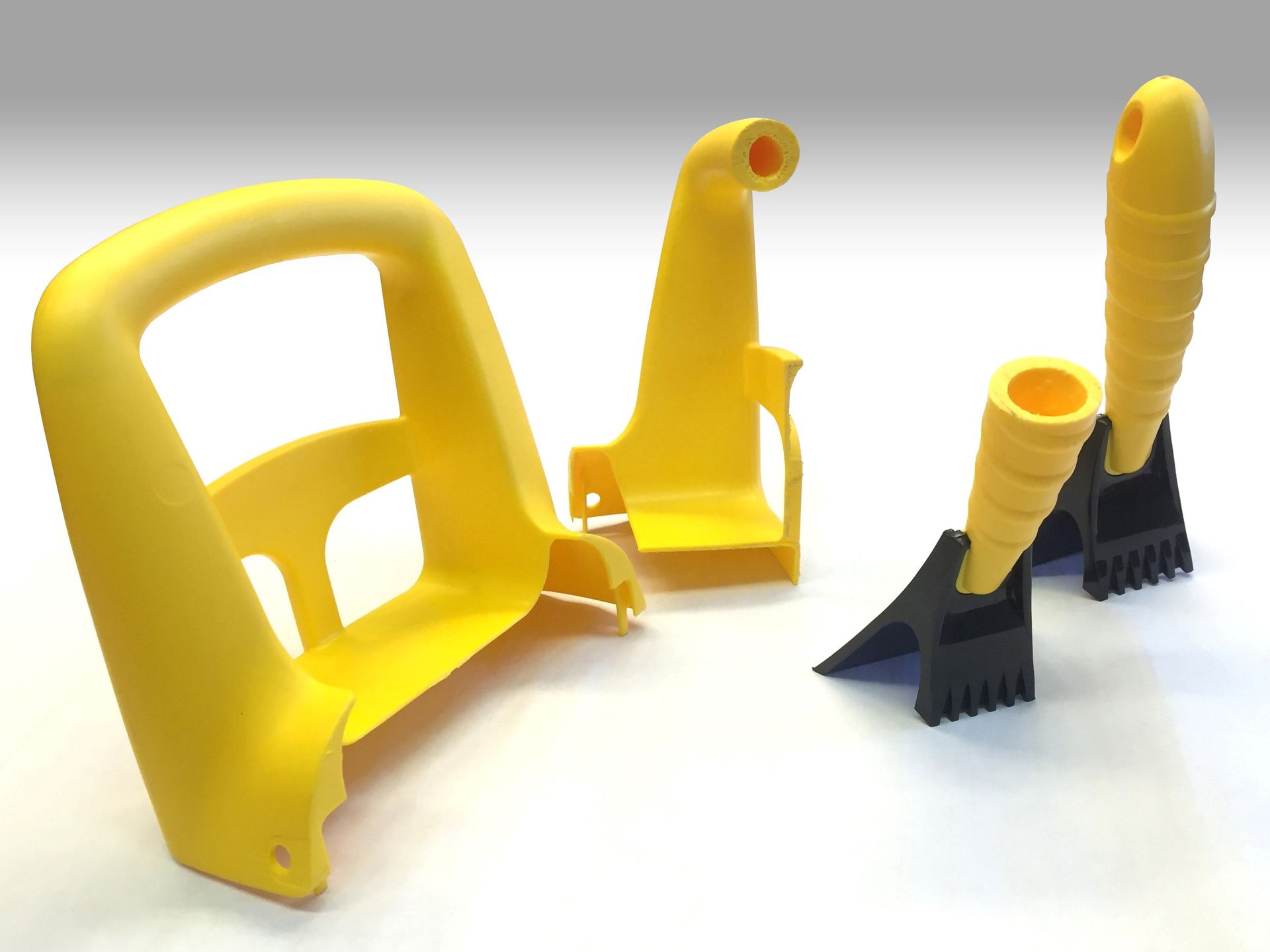
Request a Free Consultation
Learn With EnTech
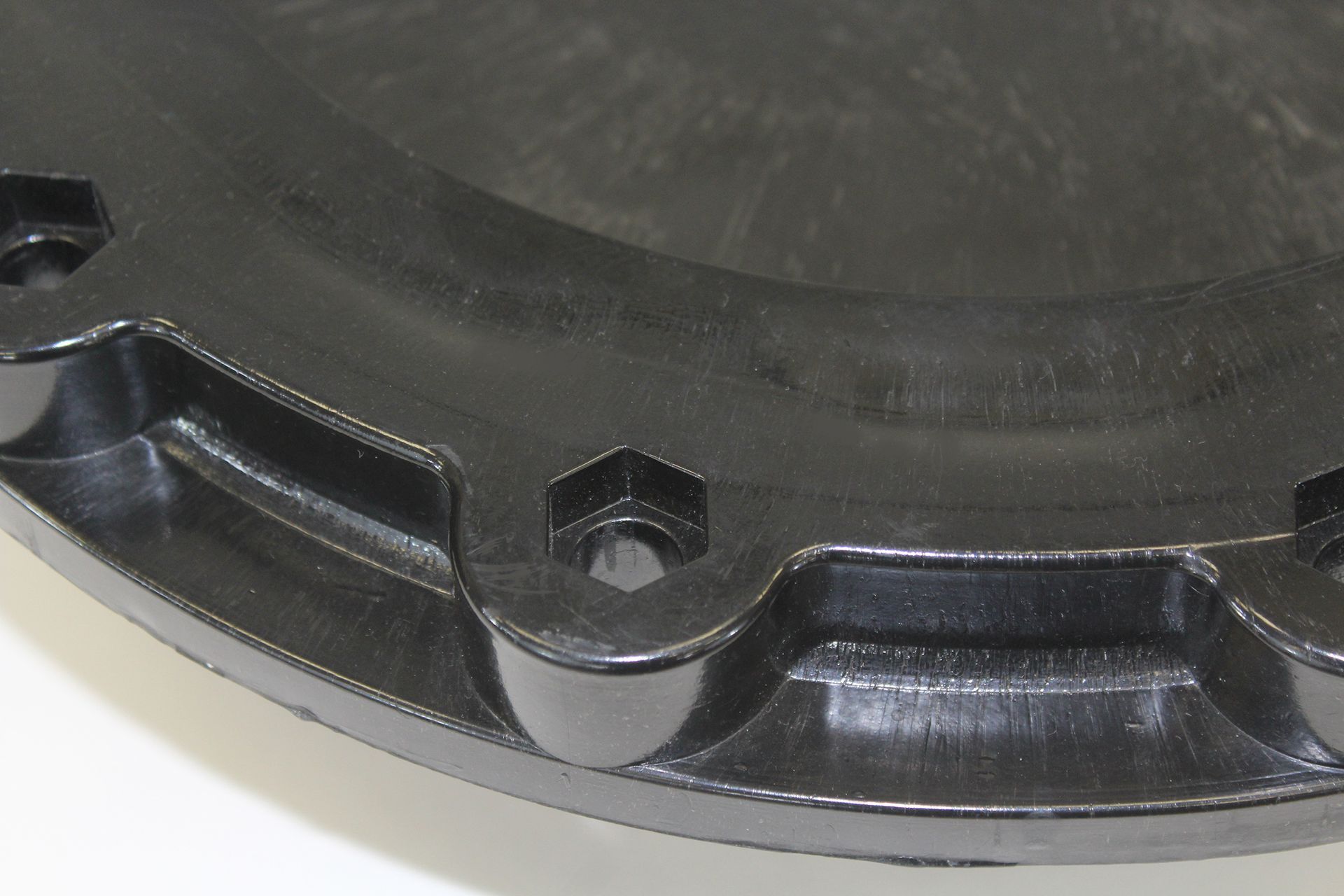
When it comes to manufacturing plastic parts, two of the most widely used processes are injection molding and compression molding. While both techniques shape materials using heat and pressure, they differ significantly in their approach, capabilities, and ideal applications. Understanding these differences is crucial for manufacturers, designers, and engineers when selecting the optimal process for their specific needs. What is Injection Molding? Injection molding is a manufacturing process where heated, molten material (typically thermoplastic) is injected under high pressure into a closed mold cavity. The process begins with plastic pellets or granules being fed into a heated barrel where they're melted and mixed by a rotating screw. Once the material reaches the proper temperature and consistency, it's injected at high pressure through a nozzle into the mold cavity. The mold is then cooled, allowing the material within to solidify, taking the shape of the mold before being ejected as a finished part. What is Compression Molding? Compression molding is a forming process where a pre-measured amount of material (often thermosetting plastics, composites, or rubber) is placed directly into an open, heated mold cavity. The mold is then closed under pressure, causing the material to conform to the mold shape while curing or vulcanizing. The process starts with a "charge" of material—typically in powder, pellet, or preform shape—being placed in the lower half of a heated mold. The upper half of the mold is then pressed down with significant force, distributing the material throughout the cavity. The combination of heat and pressure causes chemical cross-linking in thermosetting materials, creating the final cured part. Key Differences: Injection Molding vs Compression Molding Speed and Cycle Time Injection Molding typically offers faster cycle times, especially for smaller parts. Once the mold is filled, cooling happens relatively quickly, and parts can be ejected in seconds to minutes. Compression Molding generally requires longer cycle times due to the curing process needed for thermosetting materials. Parts may need to remain in the mold for several minutes to ensure complete curing. Material Compatibility Injection Molding works best with thermoplastics that can be melted and re-solidified multiple times. Common materials include polyethylene, polypropylene, ABS, nylon, and polycarbonate. Compression Molding is ideal for thermosetting materials that undergo irreversible chemical changes when heated. This includes materials like phenolic resins, epoxies, silicones, and rubber compounds. It's also excellent for fiber-reinforced composites. Part Complexity and Precision Injection Molding excels at producing complex geometries with tight tolerances, intricate details, and thin walls. The high-pressure injection allows material to flow into fine features and sharp corners. Compression Molding is better suited for simpler shapes and is particularly effective for large, thick-walled parts. While precision is good, it may not match the tight tolerances achievable with injection molding. Tooling and Setup Costs Injection Molding typically requires higher initial tooling costs due to the complexity of the molds, which must withstand high pressures and include sophisticated cooling and ejection systems. Compression Molding generally involves lower tooling costs since the molds are simpler in design and don't require the same level of precision machining or cooling systems. Typical Applications Injection Molding Applications Industrial Devices: Leveraging benefits such as durability, cost-effectiveness, design flexibility, and lightweight, injection molded plastics find extensive functional applications in various industrial sectors. Medical Devices: Diagnostic equipment housings, Medical equipment components, Syringes, IV components, and surgical instruments demand the cleanliness and precision of injection molding. Consumer Electronics : Phone cases, computer housings, connectors, and small electronic components require the tight tolerances and smooth finishes that injection molding provides. Automotive Industry : Dashboard components, interior trim, bumpers, light housings, and under-hood components benefit from injection molding's precision and efficiency. Packaging : Bottle caps, containers, lids, and disposable items are mass-produced efficiently using injection molding. Toys and Recreation : Action figures, building blocks, sporting goods, and recreational equipment benefit from injection molding's ability to create detailed, colorful parts. Compression Molding Applications Aerospace and Defense : Composite panels, radomes, structural components, and heat shields utilize compression molding's ability to process advanced composite materials. Automotive Industry : Heavy-duty components like brake pads, gaskets, electrical insulators, and composite body panels are well-suited to compression molding. Electrical and Electronics : High-voltage insulators, electrical switchgear housings, and components requiring excellent electrical properties are often compression molded. Industrial Equipment : Valve seats, pump components, industrial gaskets, and chemical-resistant parts benefit from compression molding's material versatility. Kitchen and Appliance : Heat-resistant handles, cookware components, and appliance parts that require durability and heat resistance are ideal for compression molding. Ready to Bring Your Project to Life? Both injection molding and compression molding serve crucial roles in modern manufacturing. Injection molding excels in production of complex thermoplastic parts with excellent precision, while compression molding is the preferred choice for thermosetting materials, composites, and applications requiring specific material properties. Understanding the strengths and limitations of each process enables manufacturers to make informed decisions that optimize cost, quality, and performance for their specific applications. As both technologies continue to advance, they will remain essential tools in the manufacturing toolkit, each serving distinct market needs and applications. Looking for a precision-driven partner for your next plastic manufacturing project? At EnTech Plastics, we specialize in custom injection molding—delivering high-quality, cost-effective solutions for even the most complex part designs. Whether you're developing components for industrial goods or the medical, automotive, or consumer goods industries, our expert team is ready to help turn your concept into reality. Contact us today to discuss your project requirements.
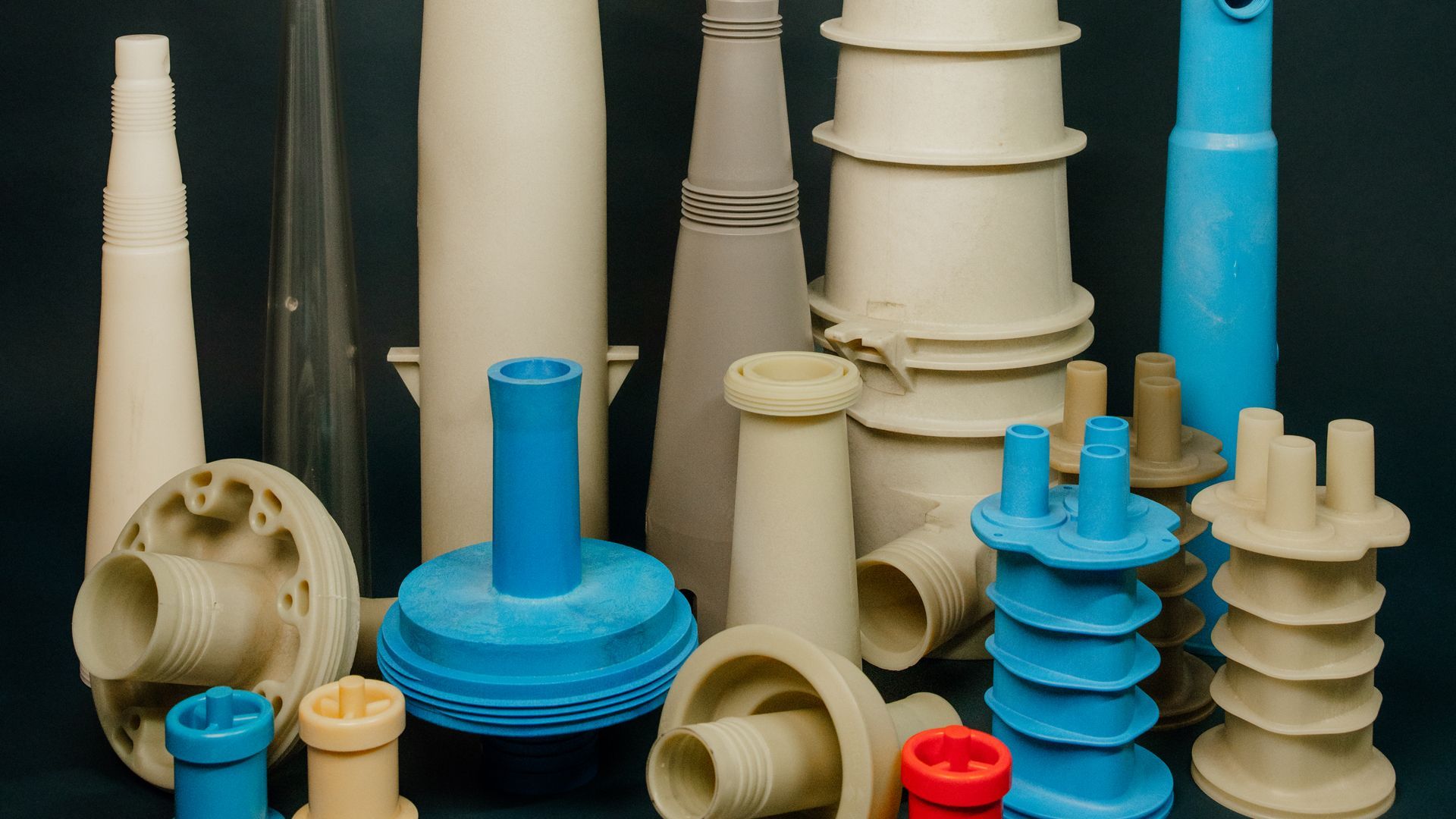
Low volume injection molding fills the critical gap between prototyping and mass production, providing engineers with a versatile manufacturing solution for production runs typically ranging from 100 to 10,000 parts. This guide explores the essential aspects of this process, helping engineers make informed decisions when specifying and designing for low volume injection molding. As manufacturing demands continue to evolve toward more agile and responsive production methods, understanding the capabilities and limitations of low volume injection molding becomes increasingly valuable for today's engineering professionals. Understanding Low Volume Injection Molding Definition and Scope Low volume injection molding typically refers to production runs of smaller quantities than traditional mass production. These can range from approximately 100-1,000 parts for prototyping and early-stage testing, 1,000-5,000 parts for pilot production or niche markets, and up to 10,000 parts for short production runs. The exact definition of "low volume" varies by industry and application, but generally refers to quantities that don't justify the high investment of hardened steel tooling used in mass production. When to Choose Low Volume Injection Molding Low volume injection molding serves multiple purposes across the product development lifecycle. It excels in functional prototyping scenarios where engineers need multiple identical prototypes for testing and validation using actual production-grade materials. This provides more accurate test results than other prototyping methods that might use different materials or manufacturing processes. It also serves as an effective bridge production solution, filling the gap between initial prototyping and full-scale manufacturing. This approach allows companies to enter the market while traditional high-volume tooling is being developed, potentially generating revenue earlier in the product lifecycle. Market testing represents another valuable application, where companies can produce limited quantities to gauge market response before committing significant resources to mass production infrastructure. For specialized components with limited market demand, low volume injection molding often provides the only economically viable manufacturing path. Many manufacturers also leverage this approach for supply chain optimization, producing parts on-demand to reduce inventory costs and effectively manage demand volatility. This just-in-time manufacturing approach can significantly reduce warehousing costs and obsolescence risks. Tooling Options for Low Volume Production Aluminum Molds Aluminum molds represent the most common tooling solution for low volume injection molding due to their excellent balance of cost, speed, and performance. Compared to traditional steel molds used in high-volume production, aluminum tooling offers 40-60% lower costs and significantly faster lead times, typically 2-4 weeks versus the 4-8 weeks required for steel tooling. The superior thermal conductivity of aluminum—conducting heat approximately five times faster than steel—results in shorter cycle times during production. This thermal efficiency allows for quicker cooling of molded parts, reducing overall production time and increasing throughput. Additionally, aluminum's softer nature makes it easier to machine, further reducing tooling costs and lead time. While not as durable as steel, aluminum molds provide sufficient durability for low to medium production volumes, typically handling between 10,000 and 100,000 shots depending on the material being molded and the complexity of the part geometry. This makes them an ideal choice for most low-volume applications where tooling cost and lead time are critical factors. 3D Printed Molds For very small production runs or rapid prototyping needs, 3D printed molds offer an innovative and increasingly viable solution. These molds can be produced at significantly lower costs, often between $100-$500 for simple geometries, and with extremely fast turnaround times measured in days rather than weeks. This approach enables engineers to quickly iterate on designs without the financial burden of traditional tooling. 3D printed molds are most effective for producing limited quantities, typically between 50-200 parts, depending on the material being molded and the complexity of the part. They work particularly well for proof-of-concept models and initial market samples where dimensional precision is less critical than speed to market. However, these molds do come with significant limitations that engineers must consider. Their limited durability restricts them to lower shot counts, they're generally restricted to simpler geometries and less demanding materials, and they provide lower dimensional accuracy compared to metal molds. Temperature and pressure limitations also constrain the range of materials that can be effectively molded with 3D printed tooling. Soft Tooling Soft tooling using materials like silicone or urethane provides another option for short production runs. These molds can be produced at lower costs than aluminum tooling and with quick turnaround times, making them suitable for projects with extremely tight timelines or budget constraints. These tools perform best with parts featuring relatively simple geometries and work well for prototyping and very short production runs, typically under 500 shots. The flexible nature of these materials can sometimes allow for parts with features that might be challenging with rigid tooling, such as limited undercuts. Engineers should be aware that soft tooling comes with significant limitations, including restricted material compatibility, less precise tolerances, and a substantially shorter lifespan compared to metal tooling. These factors make soft tooling most appropriate for early development phases rather than ongoing production. DME MUD Inserts Some manufacturers use MUD (Master Unit Die) inserts for lower volume tooling as a cost-effective alternative to full custom molds. This universal mount system uses less steel and fewer off-the-shelf components to build the mold, resulting in significant savings on tooling costs. MUD inserts offer faster changeovers for multiple parts, making them particularly suitable for part families or products with multiple variants. The ability to reuse the base while changing only the inserts provides both economic and time advantages for appropriate applications. This approach works best for smaller parts that fit within the standardized frame sizes of the MUD system. While not suitable for all applications, MUD inserts represent a valuable intermediate option between fully custom tooling and more temporary solutions like 3D printed molds. Material Selection Many thermoplastics used in high-volume injection molding are also well-suited for low-volume applications, offering engineers a broad range of options to meet specific project needs. However, successful material selection in low-volume production requires a strategic balance of several interrelated factors. The process should begin with functional requirements—ensuring that the material’s mechanical, thermal, electrical, and chemical properties align with the application. Cost is equally important, not just in terms of raw material price, but also processing conditions and cycle times, which can offset lower per-pound costs. Tooling compatibility is another key factor, especially when using aluminum molds common in low-volume runs. Abrasive materials, such as those with glass fiber reinforcement, can significantly reduce tool life and impact cost-effectiveness. Engineers should also account for post-processing needs like painting, texturing, or assembly. Selecting materials that meet aesthetic and performance standards straight out of the mold can streamline production and reduce lead times. Finally, environmental exposure—such as temperature extremes, chemicals, UV radiation, and moisture—must be considered to ensure long-term material performance. Choosing a material with the right resistance profile is critical to product durability and reliability. Design Considerations Wall Thickness - Maintaining a uniform wall thickness is essential to prevent molding defects like warping, sink marks, and internal stresses caused by uneven cooling. In low-volume production, where tooling revisions can be costly, getting wall thickness right the first time is especially important. Part Finish - Specifying the correct surface finish is key to balancing cost and performance. Highly polished finishes significantly raise tooling expenses due to the labor-intensive polishing process. For non-visible components, an as-machined finish is a cost-effective option. For moderate cosmetic needs, bead-blast texture provides a cleaner look without the high cost of polishing. Gate Location and Design - Gate placement directly affects how molten plastic flows through the mold, influencing both the quality and appearance of the part. Proper gate location ensures uniform filling and reduces the risk of weld lines or voids. Since gates leave marks, they should be positioned in low-visibility areas or where post-processing can easily remove marks or blemishes. Parting Lines - Parting lines—where mold halves meet—leave visible seams on finished parts and must be planned carefully. Avoid placing parting lines on functional or highly visible surfaces, such as sealing areas or product front faces. Instead, these lines should align with natural edges or surface transitions to minimize their appearance. Leveraging Low Volume Injection Molding Low volume injection molding offers engineers a versatile and cost-effective solution for producing high-quality plastic parts in quantities that bridge the gap between prototyping and mass production. By understanding the unique considerations, tooling options, and design principles outlined in this guide, engineers can successfully leverage this manufacturing method to accelerate product development, optimize costs, and bring innovative products to market more efficiently. EnTech Plastics specializes in low volume injection molding solutions tailored to your specific engineering challenges. Contact EnTech Plastics today to discuss your next engineering project and discover how our low volume injection molding capabilities can help you bring innovative products to market faster and more efficiently.